
Viper Wire Rope Lubricator
Viper Wire Rope equipment provides many benefits:
The Viper Rope Lubricator allows wire ropes to be safely, quickly and effectively lubricated and has the potential to extend their life significantly. Eliminating the need for manual greasing, this reduces downtime and improves equipment availability. It is a safer way to lubricate wire ropes, reduces lubricant usage, has less leakage and reduces mess.




Viper Wire Rope Lubricator Variants
Viper Mini MKII Suitable for wire ropes between 6mm to 36mm
Health Safety & Environment
The Viper WRL was developed with safety and the environment in mind. When correctly used the Viper WRL has several Health, Safety and Environment benefits:
- Every gram of grease goes on the rope
- Does not leak meaning no mess
- No wasted lubricant
- Light weight allows for safe application
- There is no direct contact with the lubricant
- The rope can be lubricated from a safe distance

The Viper Seal
What makes the viper WRL seal so special?
Viper seals are proven to have lasted for > 15,000 metres of rope.
The unique Viper seal design is at the heart of the Viper WRL package. The selected polyurethane material is wear-resistant to ensure long service life but still flexible enough to mould to the rope. This flexibility helps reduce leakage but more importantly massages the lubricant into the rope, increasing penetration of the lubricant and the protection from corrosion that this provides. Other wire rope lubricators tend to simply coat the outside of the rope. The length of the Viper Mid and Maxi collar / seal combination also increases the dwell time that the rope has with the lubricant, which also helps with application and ultimately leads to longer rope life and extended lubrication intervals
Beneficial Quality | What This Means For You |
Material |
|
Seal Design/ Rib Length |
|
Length of Seal |
|
VMRCS Manual Rope Cleaner
To achieve optimum visual inspection of wire rope assets it is critical that old lubricant and contamination is removed from the outer strands and valleys of the rope, prior to inspection. Viper WRL has revolutionised the process of cleaning ropes by combining CAD based design with manufacturing techniques and composite materials to deliver the Viper Manual Rope Cleaner Solution Kit. This kit is used in conjunction with our Viper Rope Cleaners (VRC).
Why use the VMRCS Wire Rope Cleaner
- Effectively removes external contamination on wire ropes so visual inspection of rope can take place.
- Safer for staff, reduced lubricant usage, less leakage and mess.
- One-person job – easy to install and use.
- No tools required, very easy and fast to install.
- Reduced downtime associated with rope lubrication which improves equipment availability.
- Less wear on sheaves and winch drums.
- Removes contamination in the valleys of the rope to provide improved lubricant penetration.
- Unit has two support bushes spaced well apart giving the unit a lot of stability.
Australian STS Crane – Rope being Cleaned and Lubricated
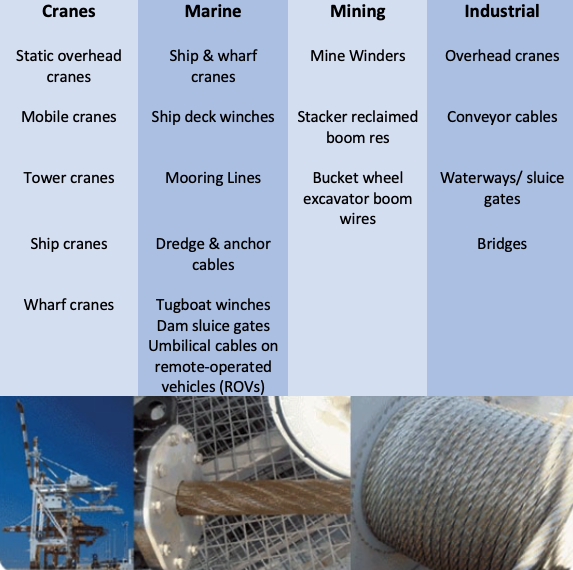
Viper Rope Cleaners
Viper Rope Cleaners enable the removal of contamination or built-up old lubricants from the wire rope prior to lubrication, improving the effectiveness of the lubrication process via the Viper WRL. Viper Rope Cleaners (VRC’s) are available in left and right hand lay, to suit 6 and 8 strand ropes and other strand configurations on request. For certain types of wire ropes where the standard Viper Rope Cleaner is not suitable the Viper ‘Smooth Bore’ rope cleaner is available.
The Smooth Bore Rope Cleaner would typically be used on hose ropes with a large number of outer strands, some nonrotational ropes, ROV cables, etc, where the valleys between the strands are minimal and do not readily facilitate a standard Viper Rope Cleaner.
The Viper Wire Rope Lubricator in Action
Lubricating Upper Section of Gottwald Crane Rope
Viper MKII In Operational and Training
Viper Mini WRL Cleaning and Lubricating Mooring Lines on Tanker
Correct Lubrication
Wire rope lubricants have three principal functions:
Reducing the friction as the individual wires move over each other, providing corrosion protection in the core and inside wires and on the exterior surfaces, and preventing abrasive wear.
Abrasive wear can occur on the inside and outside of the rope, depending on the operating environment. Abrasive wear usually reduces rope diameter and can result in core failure and internal wire breakage.
Picking the correct heavy-duty industrial wire lubricant is critical to prolonging wire rope life.
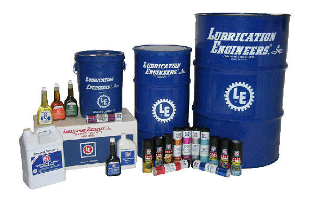


Solution
Pure Lubrication is the authorised UK distributor for Lubrication Engineers Inc, supplying LE products and services.
Lubrication Engineers has formulated industrial wire rope lubricants built to meet the challenges, whether you are looking for a penetrating or coating lubricant.
When properly applied to the wire rope, their outstanding adhesive strength helps them remain on the rope; maintain a strong lubricating film between wires and strands; and resist oxidation, water and abrasive contaminants; all while remaining pliable in use.
Get in Touch
To find out more, contact our friendly team who are here to help and will be delighted to tailor a wire rope solution to your individual requirements along with providing advice on approved lubricants to use for your specific application. Call us on 0800 612 3536 or email sales@purelubrication.co.uk